Polishing machines are essential tools in various industries such as automotive, jewelry, metalworking, and even woodworking. These machines are designed to smoothen the surface of a material and bring out its natural shine. But have you ever wondered how these machines work and what makes them so effective? In this article, we will explore the science behind the shine of polishing machines.
Understanding the Polishing Process
Before we dive into the details of how polishing machines work, let’s first understand the polishing process itself. Polishing is the process of removing surface imperfections such as scratches, roughness, and other defects that can affect the appearance and performance of a material. The goal of polishing is to create a smooth and uniform surface that reflects light evenly, resulting in a shiny finish.
Polishing involves the use of an abrasive material that is applied to the surface of the material being polished. The abrasive material can be in the form of a liquid or paste, and it can contain various abrasive particles such as diamond, alumina, or silicon carbide. The abrasive particles work by grinding and cutting away the surface of the material, smoothing out the imperfections and creating a smoother surface.
The polishing process can be done manually using a polishing cloth or buffing wheel, or it can be done using a machine. Polishing machines are more efficient and effective in creating a uniform and consistent finish, especially for larger or more complex surfaces.
How Polishing Machines Work
Polishing machines work by using a rotating polishing head that applies pressure and abrasive material to the surface being polished. The polishing head can be made of different materials such as cloth, felt, or foam, depending on the type of material being polished and the desired finish.
The polishing head rotates at a high speed, typically between 1000 to 3000 revolutions per minute (RPM), depending on the type of machine and the material being polished. As the polishing head rotates, it applies pressure and the abrasive material to the surface being polished, grinding away the imperfections and creating a smoother surface.
Different types of polishing machines use different mechanisms to apply pressure to the polishing head. Some machines use a pneumatic system that uses air pressure to apply pressure to the head, while others use a hydraulic system that uses fluid pressure. Some machines also use a weighted system that applies pressure to the head using the weight of the machine itself.
Choosing the Right Polishing Machine
Choosing the right polishing machine depends on several factors, such as the type of material being polished, the desired finish, and the size and complexity of the surface being polished. There are different types of polishing machines available in the market, each designed for specific applications.
For example, in the automotive industry, a rotary polisher is commonly used for polishing car paint. This type of machine has a circular polishing head that rotates at a high speed, and it is designed to remove scratches and imperfections in the paint while creating a glossy finish. In the jewelry industry, a vibratory tumbler is commonly used for polishing small parts and components. This type of machine uses a vibrating motion to agitate the abrasive material and the parts being polished, creating a uniform and shiny finish.
The Science behind the Shine
The shine created by polishing machines is not just a result of removing surface imperfections. The science behind the shine is based on the way light interacts with the surface of the material being polished.
The science behind the shine also depends on the type of material being polished and the properties of the abrasive material. The abrasive particles in the polishing compound remove a very thin layer of the surface, creating tiny scratches or grooves. These scratches or grooves are then gradually reduced in size by using a finer abrasive compound. As the scratches become smaller, the surface becomes smoother and more reflective. The final result is a smooth and uniform surface that reflects light evenly, creating a shiny appearance.
In addition, the properties of the polishing compound, such as the size and shape of the abrasive particles, the hardness of the particles, and the concentration of the abrasive material in the compound, all affect the final result. For example, a compound with larger abrasive particles may remove surface imperfections more quickly, but may also leave deeper scratches that require more polishing to remove. On the other hand, a compound with smaller abrasive particles may require more time to polish but may create a smoother and shinier finish.
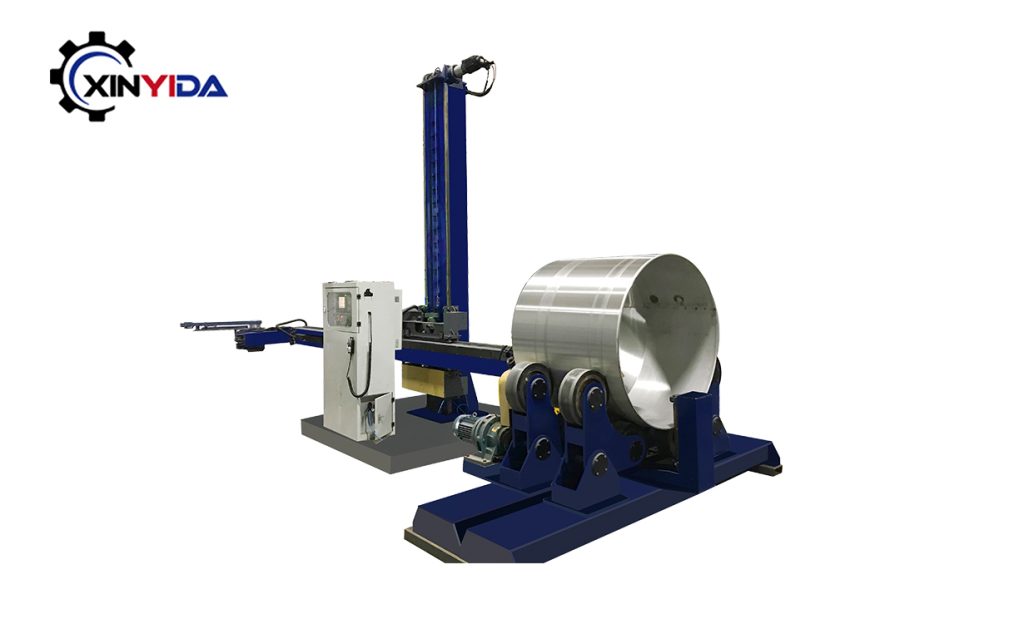
tank shell polishing machine
In conclusion, polishing machines are powerful tools that use the science behind the shine to create a smooth and shiny surface on various materials. The polishing process involves removing surface imperfections and creating a uniform and reflective surface. The properties of the abrasive material and the polishing compound, as well as the type of polishing machine used, all affect the final result. By understanding the science behind the shine, you can choose the right polishing machine and compound for your specific application and achieve the desired result.